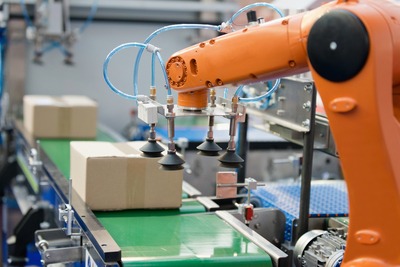
Packaging machinery is the backbone of any production line, responsible for efficiently and accurately packaging products. To ensure optimal performance and longevity of these machines, regular maintenance is crucial.
In this article, we will explore the importance of proactive maintenance for packaging machinery, highlighting the benefits it offers in minimizing downtime and avoiding costly repairs. Here are some best practices to consider:
-
Set Up a Preventive Maintenance Schedule:
• Create a comprehensive maintenance schedule that includes regular inspections, cleaning, lubrication, and adjustments.
• Follow the manufacturer's guidelines for specific maintenance intervals.
• Keep detailed records of maintenance activities, including dates, tasks performed, and any issues found.
-
Perform Routine Inspections:
• Regularly inspect all components of the packaging machinery, such as belts, chains, motors, gears, and electrical connections.
• Look for signs of wear, damage, or misalignment.
• Check for loose fasteners or unusual vibrations during operation.
• Address any issues promptly to prevent further damage or potential breakdowns.
-
Keep It Clean and Lubricated:
• Clean the machinery regularly to remove dust, debris, and product residue that can affect performance.
• Use recommended cleaning methods and solutions from the manufacturer.
• Lubricate moving parts according to the manufacturer's specifications, using the recommended lubricants.
• Ensure proper lubrication to reduce friction, minimize wear, and extend the lifespan of critical components.
-
Train and Educate Operators:
• Provide comprehensive training to operators on proper operation and basic maintenance procedures for the packaging machinery.
• Emphasize the importance of regular inspections, cleaning, and reporting any abnormalities or malfunctions.
• Encourage operators to be proactive in identifying and addressing minor issues before they become major problems.
-
Implement Condition Monitoring:
• Utilize advanced technologies, such as sensors and monitoring systems, to track the performance and condition of packaging machinery in real-time.
• Monitor key parameters like temperature, vibration, pressure, and power consumption to identify potential issues early.
• Analyze data collected from condition monitoring to detect patterns, predict maintenance needs, and optimize machine performance.
-
Collaborate with Equipment Suppliers:
• Build a good relationship with machinery suppliers to benefit from their expertise and support.
• Seek guidance on maintenance best practices specific to your equipment.
• Stay informed about software updates or firmware upgrades that can enhance performance and address known issues.
-
Plan for Spare Parts and Backup Equipment:
• Maintain an inventory of critical spare parts to minimize downtime in case of unexpected failures.
• Work closely with equipment suppliers to identify the most commonly needed spare parts.
• Consider having backup machinery or arrangements for temporary replacements during major repairs.
-
Regularly Review and Improve Maintenance Procedures:
• Continuously evaluate the effectiveness of your maintenance procedures and seek feedback from operators and maintenance personnel.
• Identify areas for improvement and make necessary changes to optimize maintenance practices.
• Stay updated with industry advancements and emerging technologies that can enhance maintenance processes.
Regular maintenance is vital for ensuring optimal performance and longevity of packaging machinery. By following these simple best practices and adopting a proactive maintenance approach, you can reduce downtime, avoid expensive repairs, and maximize the efficiency and reliability of your packaging operations. Remember, investing time and effort in maintenance now will pay off in the long run by reducing operational disruptions and improving overall productivity.